1.1 Introduction |
Textile fibers have been used to make cloth for several thousand years. First manufactured fiber was produced commercially on 1885 and was produced from fibers of plants and animals. Wool, flax, cotton and silk were commonly used textile fibers. Textile fibers are characterized by the flexibility, fineness and large length in relation to the maximum transverse dimension. On the basis of origin fibers can be classified broadly into three types:
|
I. |
Natural fibers: Fibers which grow or develop and come from natural resources like plant and animals. |
II. |
Manufactured (or man-made) fibers: Fibers produced by industrial processes, whether from natural polymers transformed upon the action of chemical reagents or through polymers obtained by chemical synthesis (synthetic fibers). |
III. |
Mineral Fibers: Asbestos is the only naturally occurring mineral fiber that was used extensively for making industrial products but is now restricted due to its suspected carcinogenic effect. |
|
General properties with regard to fiber properties
|
The general considerations provide the background information upon which the explanations of a fiber’s properties are based.
|
|
Morphology or physical structure of textile fiber includes the study of the size, shape and structure of textile fiber, by observing the fiber using a microscope and the relationship between these properties. Fiber’s morphology influences fabric characteristics and performance and the process that will be used in producing a finished fabric.
|
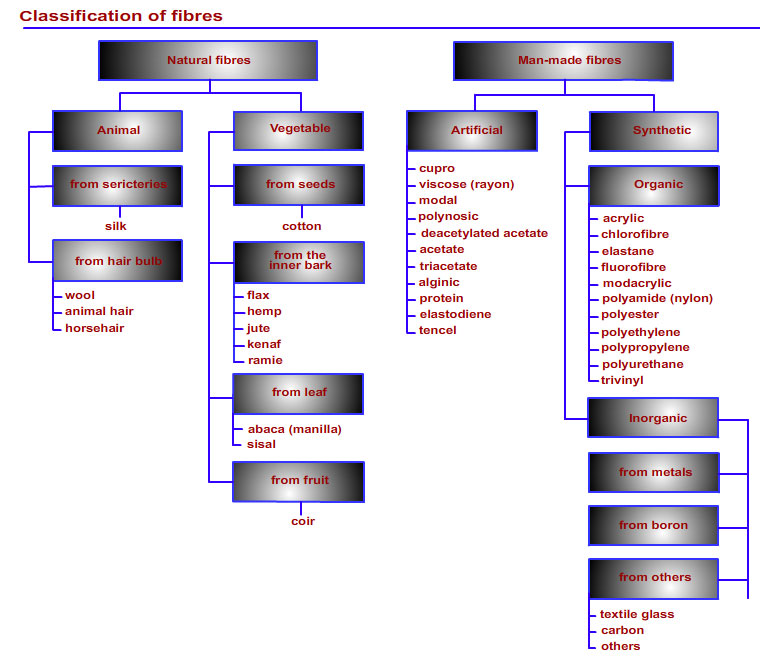 |
Fig1: Classification of fibers [1] |
|
A. Fiber length |
Fibers are sold as staple, filament or filament tow. Basic differences between these are explained below: |
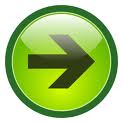
|
A fiber or staple fiber is a unit of matter which is usually at least 100 times longer than it is thick. They are measured in inches or centimeters range in length from 2 to 46 cm (3/4 inch to 18 inches). Among all the natural fibers, which are found in staple form, silk is an exception. Fibers are several thousand times longer than their thickness. The thickness of fibers ranges from about 10μm to 50μm. |
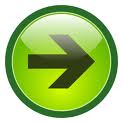 |
A filament is a very long, continuous fiber strand of indefinite length. The length of filaments may range from a few hundred meters, as in the case of silk, to several kilometers in the case of man-made fibers. The thickness of filaments is similar to that of fibers. They exist either in monofilament or multifilament. |
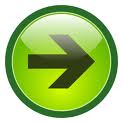 |
Filament tow is a loose rope of several thousand fibers, is crimped or textured, and cut to staple length. |
|
Fibers or filaments finer than about 10μm tend to become too delicate or fragile for ready conversion into a yarn structure. Fibers or filaments exceeding about 50μm in thickness easily give a yarn structure which is too coarse and too thick for comfort when used as apparel.
|
B. Diameter |
Fiber diameter decides a fabric’s performance and hand (how it feels). Large diameter fibers are crisp, rough and stiff. Fine fibers are soft and pliable and fabric made of them drape more easily. In natural fibers, fineness is one factor which determines fine quality fibers of better quality. Fineness is measured in micrometers (a micrometer is 1/1000 millimeter or 1/25,400 inch). The diameter range for natural fibers is 16 to 20 micrometers for cotton, 12 to 16 for flax, 10 to 50 for wool, and 11 to 12 micrometers for silk.
|
C. Fiber length to fiber breadth (diameter) ratio |
This ratio decides suitability of a fiber for spinning into yarn, provided, it first meets the fiber length and thickness requirement. The smallest appropriate ratio of fiber length to fiber breadth (thickness) is about 350:1. Ratio less than this indicate a fiber which will not permit twisting of fiber into a yarn structure. But fiber ratio of 1000:1 or more spins into a useful yarn. Fineness of manufactured fibers is measured as denier or tex.
|

|
Denier is the weight in grams of 9000 meters of fiber or yarn. It gives the fineness or coarseness of fibers. Small numbers refer to fine fibers; large number describes coarse fibers. It is related with end use of fiber. |
 |
Tex is the weight in grams of 1000 meters of fiber or yarn. |
|
Textile fibers range from 1 to 7 denier. Carpet fibers ranges from 15 to 24 denier. Industrial fibers show the broad range from 5 to several thousand, depending on the use. Denier per filament (dpf) describes fiber size; it is often used when describing or specifying yarns. Dpf is calculated by dividing the yarn size by the number of filaments: 80 denier yarn/ 20 filaments equals to 4 denier per filament. Fine cotton, wool has 5 to 8 denier; carpet wool is 15 denier.
|
D. Color
|
White or colorless fibers and filaments are preferred. Color of natural fibers and delustred man-made fibers are white to off-white. Bright-lustre man-made fibers and filaments are colorless because they are translucent. Reason of preference for white or colorless fibers is they can be dyed or printed with any hue of color.
|
E. Translucency |
A translucent fiber will transmit light but is not transparent. Silk and manmade fibers, when bright-lustred, are translucent. Cotton, flax and wool are also delustred man-made fibers, tend to be opaque; but when these fibers are made into light to very light weight fabrics, then their fineness makes them translucent.
|
F. Luster |
Luster results from the way light is reflected from surface. This is a subjective measure of the reflection of incident light from a fiber, filament or textile material. The more lustrous a fiber, the more evenly does it reflect the incident light. The less lustrous or dull fiber or filament, the less evenly does it reflect or the more does it scatter the incident light. Cotton has a convoluted fiber structure and wool a serrated surface structure, the result is that these fibers scatter the incident light, and are thus dull fibers. The more regular and even surface structure of flax, mercerized cotton and silk gives these fibers a distinct luster, due to the even reflection of incident light. The irregular specks of delustering agent contained within delusterd man-made fibers scatter sufficient of the incident light to make these fibers or filaments duller than their bright luster equivalents. A preference for non-lustrous or dull textile fibers and filaments exists. This is evident in the predominance of dull-lusterd or non-lustrous apparel and household textiles normally purchased and used by consumers. Cross-section of fiber effects upon luster and other physical fiber properties.
|
i.Circular cross section of fiber |
|
Fig 2: circular cross section of fiber [2] |
|
Circular cross-sectional shape imparts strong luster to the fiber or filament because the incident light is reflected so unevenly, this tends to result in a rather harsh, strong luster. Harsh luster is because when the fiber or filament may be twisted in the yarn or fabric; its circular shape allows reflecting the same amount of incident light despite the unevenness of its reflection. |
Circularcross-sectional shape results in high bending stiffness, rigid, least flexible and least pliable fiber because of its regular diameter. Smooth regular surface of fiber results in a waxy, slippery handle and causes the fiber or filament to make maximum contact with the skin. This is aesthetically undesirable.
|
ii.Oval, dog- bone or bean type and triangular type cross section |
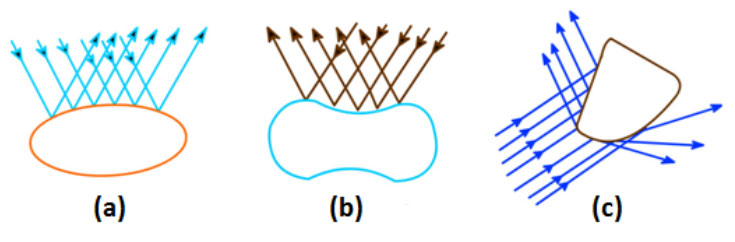 |
Fig 3: (a) oval type (b) dog-bone or bean type (c) triangular type [2] |
|
These cross-sectional shapes should give strong luster as they can reflect the incident light most evenly. But when the fiber or filament would be twisted upon itself in the yarn and fabric, the incident light is not reflected as evenly as expected and it results in softer luster. |
These cross-sectional shapes result in the least bending stiffness, most pliable, most flexible, most supple fiber. Smooth regularity of their surfaces may impart slippery handle and cause the fiber or filament to make maximum contact with the skin which is aesthetically undesirable. The distinct edges of the more triangular cross-sectional shape create more friction between fiber or filament and the skin giving it a crisper, less way, less slippery handle. |
iii. Trilobal or multilobal shaped cross section |
|
Fig 4: (a) trilobal type (b) multi-lobal type [2] |
|
These cross-sectional shapes reflect the incident light unevenly. Theoretically they impart a distinct and very bright sparkle or glitter due to the reason that when the fiber or filament is twisted upon itself in the yarn and fabric the already irregular reflection of incident light is further reduced which creates only ‘bursts’ of evenly reflected incident light from the less curved surfaces of the cross-sectional shape as seen along the length of the fiber, filament, yarn or fabric. The tri-lobal cross–section possesses the greatest degree of sparkling luster as the number of lobes in the cross-sectional shape is increased and becomes multi-lobal. The incident light is scattered to such an extent on reflection that no sparkle and only a very dull luster can be seen. |
Multi-lobal and trilobal cross-sectional shapes results in not stiff, easy to bend, pliable, flexible with a soft handle fibers. The handle may also be crisp because the lobes may create increased friction between the fiber, filament and the skin. The regularity and evenness of the lobes may still, give a smooth-and slippery handle of fiber and fabric.
|
iv. Irregular cross section |
|
Fig 5: Irregular cross section [2] |
|
v. Titanium dioxide |
|
Fig 6: Titanium dioxide [2] |
|
Titanium dioxide is a white grounded fine powder to have particle size of less than one micrometer. It is used in the spinning solution of man-made fibers as a delustring agent. The various different shapes of the titanium dioxide particles results in the reflection of the light at random or in no particular order. Thus when they are within the extruded filament, it will display a reduced luster. For the manufacturing of semi-luster filaments about half a per cent of titanium dioxide has to be mixed to the spinning solution. For the manufacture of dull luster filaments and staple fiber, up to two per cent of titanium dioxide may have to be added to the spinning solution. |
|
|
|
|
|
|
References |
-
http://textlnfo.wordpress.com/2011/10/24/classification-of-textile-fibers-according/ (accessed on 20 October 2013)
-
E.P.G. Gohl, L.D. Vilensky, Textile science, Longman Cheshire Pty Limited, 1980
|
|
|
|
|
|